На пути к женевской печати
Когда Richemont получил контроль над Roger Dubuis, многие удивились такому приобретению, ведь эта молодая и весьма эпатажная марка с трудом вписывалась в компанию аристократических брендов люксового концерна
Когда Richemont получил контроль над Roger Dubuis, многие удивились такому приобретению, ведь эта молодая и весьма эпатажная марка с трудом вписывалась в компанию аристократических брендов люксового концерна. Но специалисты сразу поняли, что Richemont привлекли вовсе не дизайнерские эксперименты Карлоса Диаса, а его другое, менее афишируемое детище – мануфактура в Мейрине.
Новое здание мануфактуры Roger Dubuis было открыто в 2005 году, и тогда же компания заявила о запуске мануфактуры полного цикла. В честь чего в том же году публике было представлено сразу 5 (!!!) совершенно новых собственных калибров.
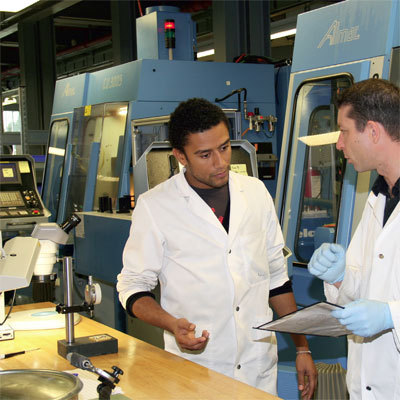
Но публика засомневалась – мало ли кто в наши дни называет себя мануфактурой. Тем более что на фабрику в то время особенно не приглашали: вместо этого журналистам был выдан красочный буклет с картинками, который на первой же странице сообщал, что за год на мануфактуре Roger Dubuis просверлили два миллиона дырок – удивительная информация, заставившая сомневаться в адекватности ее авторов. И опять же в реальности самой мануфактуры.
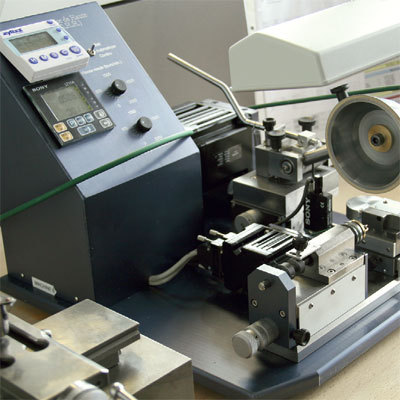
Но время шло, у компании сменились владельцы, пурпурные кресты с бриллиантами были вытеснены двойными турбийонами и другими усложнениями, которые наглядно свидетельствовали: Roger Dubuis – часовой производитель высокого класса. Осталось дело за малым. Увидеть процесс производства собственными глазами.
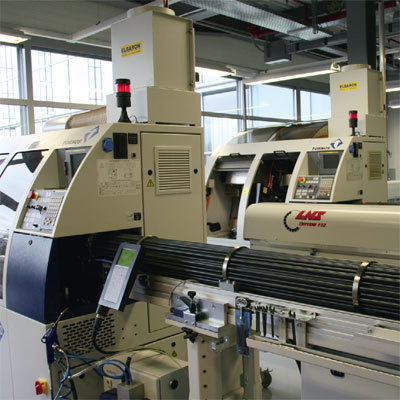
На фабрике Roger Dubuis в Мейрине нас встретила абсолютная открытость, готовность ответить на любые, даже самые
каверзные вопросы и – вы не поверите – запах масла! Нет, не оливкового, а самого настоящего машинного, подтверждающего, что мы попали на действительно серьезное производственное предприятие. Ведь под словом «мануфактура» здесь понимают именно фабрику полного цикла, занимающуюся не просто финальной сборкой часов, но и производством всех компонентов механизма, вплоть до балансов и мельчайших винтов.
Царство станков
350 сотрудников четырехэтажного стеклянного здания выпускают 2 000 штук механизмов в год. Получается по шесть механизмов на человека – меньше, чем делал ремесленник в доэлектрическую эпоху… Мало? А теперь давайте вспомним, что все 100% механизмов Roger Dubuis несут клеймо Geneva Seal, что означает высочайшее качество финишной обработки каждой мельчайшей детали механизма.
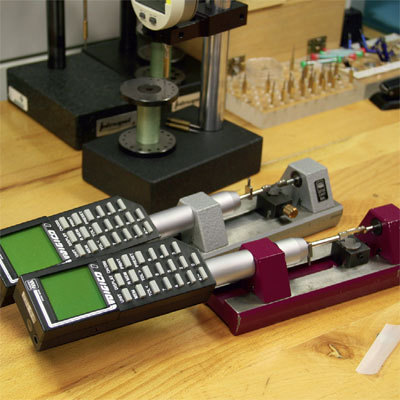
Снятые фаски мостов и платин, полированные колеса, ажурованные мосты – это лишь три из полутора десятка критериев, которым должен удовлетворять механизм, чтобы на нем появилось заветное клеймо качества. А каждый их этих критериев – это колоссальное количество труда лучших мастеров.
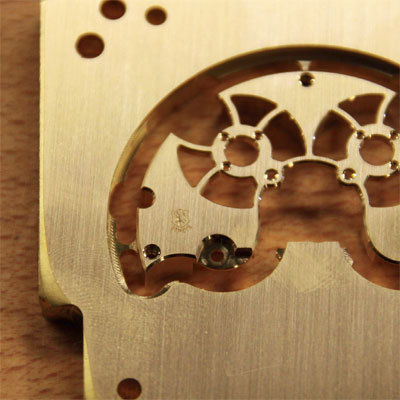
В зависимости от сложности механизма на изготовление всех деталей требуется от 70 до 200 часов работы, еще столько же – на декорирование и до 50 часов – на сборку. Итого – 450 часов, или без малого три месяца работы опытнейших мастеров над всего одним экземпляром механизма!
Весь первый этаж стеклянного здания заселен большими и маленькими станками и обрабатывающими комплексами – самыми совершенными из имеющихся в мире
«Неужели до сих пор не придумали станка, который бы выполнил всю необходимую работу?» – спросите вы. Отчего же, местами придумали. Фабрика Roger Dubuis была построена в 2005-м, и по уровню оснащения является одной из самых современных в отрасли. Весь первый этаж стеклянного здания заселен большими и маленькими станками и обрабатывающими комплексами – самыми совершенными из имеющихся в мире.
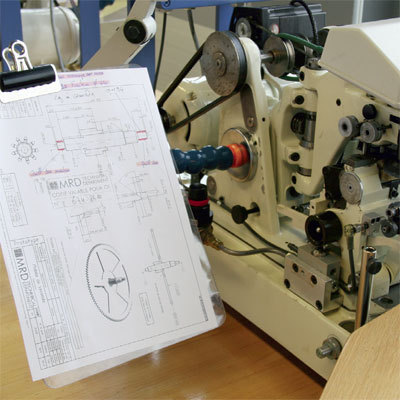
Вот аппарат, чем-то похожий на осьминога, превращает стальные прутья-щупальца в миниатюрные трибы и колеса. Чуть поодаль управляемые компьютером пятикоординатные обрабатывающие центры вытачивают самую сложную деталь часов – платину. Кстати, как это – пятикоординатные, ведь пространство описывается всего тремя? Оказывается, еще две степени свободы нужны станку, чтобы выбирать отверстия не только снаружи, но и внутри заготовки, создавая за один цикл деталь практически любой конфигурации. Например, за один проход он изготавливает платину модели Double Tourbillon, включая не только все выемки и отверстия, но и собственно «женевское клеймо».

Различные автоматы и полуавтоматы филигранно вырезают детали сложнейших форм, ажуруют мосты, нарезают мельчайшие, едва различимые глазом винты. Но в финале все это попадает с первого этажа, царства станков, на второй – в руки людей…
Печать ручного труда
Автомат – отлично! Но контроль ключевых параметров детали после каждой операции проводит человек. Ведь отклонение в расположении отверстий всего на 4 микрона может привести к тому, что зубья колесной передачи просто заклинят (оцените точность: толщина человеческого волоса – 80 микрон!). Поэтому каждая деталь проверяется на соответствие глубины и расположения отверстий.
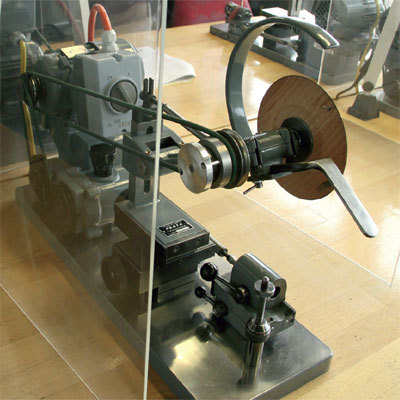
Кстати, как можно быстро проверить правильность расположения десятка отверстий на сложной детали? Для этого, а также для проверки конфигурации мостов и платин часовщики используют специальные проекторы. Мастер кладет деталь на подсвеченный столик, и увеличенная в 50 раз тень от нее попадает на матовый экран. Остается совместить с тенью прозрачный шаблон, и малейшие несоответствия станут видны невооруженным глазом. Глазом человека – потому как без него здесь пока никак.
Не обходятся без ручного труда и все операции декорирования, будь то снятие фасок на мостах, платинах или колесах, полировка, ажуровка. Интересно, что все они выглядят очень простыми внешне, но на самом деле требуют высочайшей квалификации и сосредоточенности мастера.
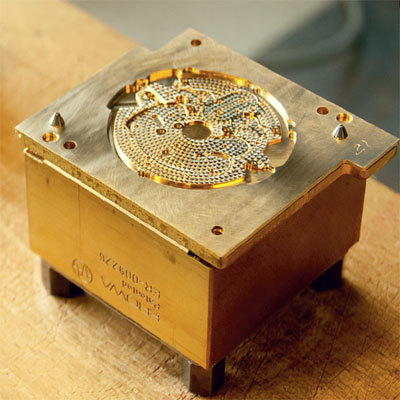
Например, знаменитый узор «перлаж» сперва наносится на платину станком. Но тот не может «дотянуться» до отдельных участков детали, расположенных в выемках и углублениях, и не чувствует структуры металла. Поэтому после такой «грубой» ажуровки за дело берется человек и подправляет все недочеты автомата. Работа с виду несложная, но требует значительного опыта: чуть более сильное нажатие – одна из «жемчужин» станет заметно ярче других, и деталь отправится в корзину.
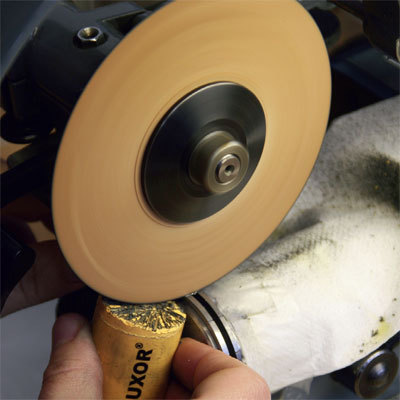
Или возьмем полировку трибов – мельчайших шестеренок, нанизанных на оси колес. Чтобы часы ходили идеально равномерно, зубья трибов должны быть тщательнейшим образом отполированы.
Качество полировки мастера определяют на слух. Разница в звучании готового колеса и бракованного столь ничтожна, что уловить ее не способны ни ухо журналиста, ни самый совершенный станок
А полируются они с помощью вращающегося деревянного диска. Мастер устанавливает ось с трибом в держатель, где тот может свободно вращаться, включает станок и опускает вращающийся диск на триб. Вращаясь, диск полирует канавку между двумя зубьями и их поверхности. Кто-то посмотрит на фото и спросит: а почему диск треснутый и зачем в него вставлена зубочистка?
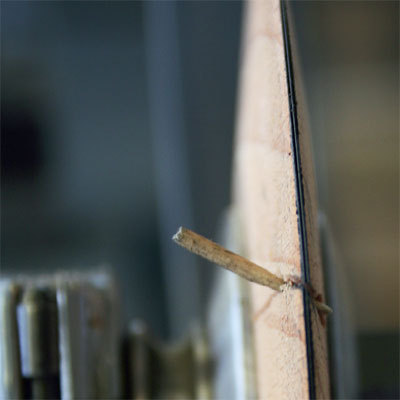
О, это волшебная зубочистка! Трещина на диске сделана преднамеренно, а зубочистка вставлена в нее так, чтобы «развести» меж собой стороны диска на расстояние, равное шагу между зубьями триба. Вращаясь, при каждом обороте диск зацепляет новый зуб триба, поворачивает его, и так перебирает и обрабатывает все зубья до одного. Представляете, каким опытом нужно обладать, чтобы «ступенька» точно соответствовала шагу миниатюрной шестеренки?
350 сотрудников четырехэтажного стеклянного здания выпускают 2 000 штук механизмов в год. Получается, по 6 механизмов на человека – меньше, чем делал ремесленник в доэлектрическую эпоху… Мало? А теперь давайте вспомним, что все 100% механизмов Roger Dubuis несут клеймо Geneva Seal
Но больше всего поражает участок полировки колес. Здесь нет сложного оборудования, а сама работа кажется предельно простой: задача мастера заключается в том, чтобы аккуратно прикладывать колесо к вращающемуся Л-образному барабану. Но хитрость заключается как раз в слове «аккуратно». Нажмешь чуть сильнее – есть риск деформировать деталь, чуть слабее – изменится рисунок.
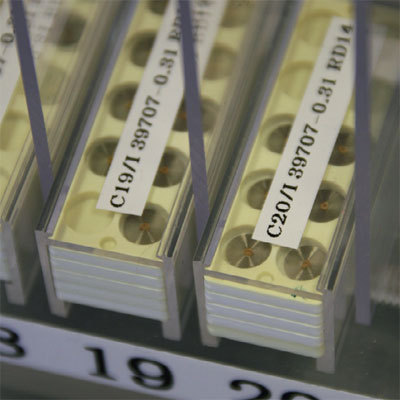
Так вот, необходимое усилие и качество полировки мастера Roger Dubuis определяют… на слух. Заготовка, готовое колесо и бракованное звучат чуть-чуть по-разному – причем разница эта столь ничтожна, что уловить ее не способны ни ухо журналиста, ни самый совершенный станок. За смену мастер может отполировать не более 70 колес, а переналадка на новый тип детали занимает до половины рабочего дня. Вы думаете, при этом мастер что-то делает с оборудованием? Нет, он просто «приучает» свое ухо к новому звуку…
Почерк мастеров
Рассказывать про мануфактуру Roger Dubuis можно еще очень долго. Например, про цех эмалевой росписи – да-да, уникальные эмалевые циферблаты Roger Dubuis делаются здесь же, в Мейрине.
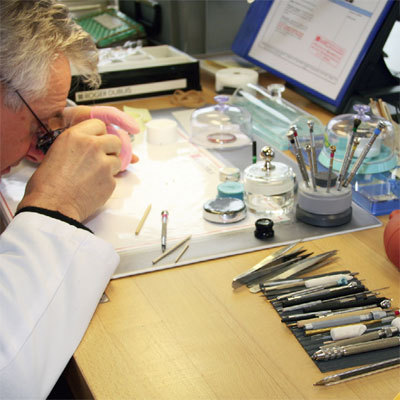
Или про еще недавно засекреченный участок, на котором изготавливают спирали баланса – компания действительно является полностью независимой в производственном отношении. Про уникальных мастеров, чьими руками наносится гравировка. Что ж, руководство Richemont было абсолютно право: упускать такой лакомый кусочек, как эта фабрика, было просто нельзя. Тем более что потенциал мануфактуры гораздо выше потребностей сегодняшней марки Roger Dubuis – в Мейрине уже делают механизмы для других компаний концерна. Для каких? На этот вопрос здесь отвечают улыбкой и рекомендуют присмотреться к стилю обработки деталей. Ведь логотип на механизме может поменяться, а вот почерк мастеров Roger Dubuis останется неизменным.
Опубликовано в журнале "Мои Часы" №3-2010